Textile dyeing and printing process
In the printing and dyeing industry, according to different raw materials, different yarn types, different fabric structures, and different printing and dyeing requirements, the process flow is not a completely fixed model, such as chemical fiber textile printing and dyeing, wool textile printing and dyeing, silk reeling in the silk industry Weaving, dyeing and finishing are quite different, and there is basically no way to learn from them.
Let's first understand the conventional processes in the three industries of spinning, weaving, printing, dyeing and finishing:
The main process of spinning process: cleaning, carding, combing, drawing, roving, spun yarn
The main process of weaving technology: winding, warping, sizing, threading, weaving, finishing
Take cotton as an example to share the conventional cotton textile dyeing and printing process.
Singeing process
After the gray cloth enters the printing and dyeing factory, it first needs to go through the processes of inspection, turning, batching, blank matching (blanket matching: the front and back of two gray fabrics are put together on the same side) and seam, and then singeing process.
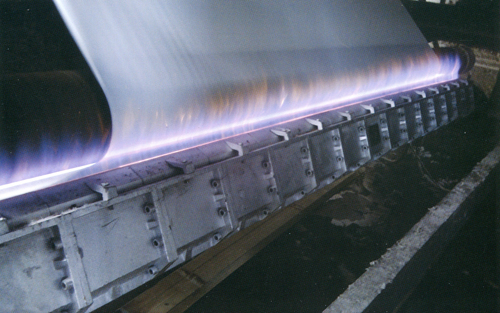
- The purpose of singeing is to burn off the fluff on the cloth surface to make the cloth surface clean and beautiful, and to prevent uneven dyeing and printing defects due to the presence of fluff during dyeing and printing. Improve the gloss of the cloth surface and improve the finish.
- Improved anti-pilling properties (especially polyester fabrics)
Cold rolling: a process after singeing, the gray cloth needs to be cooled for more than 20 hours.
Desizing, scouring, bleaching
In order to increase the wear resistance, smoothness and antistatic properties of warp yarns in weaving, increase the strength and improve its weavability, sizing is carried out before weaving. The size on the gray cloth not only affects the water absorption performance of the fabric, but also affects the quality of dyed and finished products, and will increase the consumption of dyeing chemicals, so it is necessary to use desizing enzyme TS-231 to remove the size, this process is called desizing.
Remove fiber impurities (natural impurities, artificial impurities), improve fabric processing performance, improve wetting performance, and can be treated with scouring agent TS-GLT. This process is called scouring
Bleaching process: After the cotton fabric is scoured, because there are natural pigments on the fiber, its appearance is not white enough, and it will affect the vividness of the color when it is used for dyeing or printing. The purpose of bleaching: to remove pigment and improve whiteness as the main
Mercerizing
Cotton woven fabrics treated with concentrated alkali solution can give silky luster to the surface, and more importantly, improve the dimensional stability. This process is called Mercerizing
The meaning of mercerizing treatment:
- Improved dimensional stability and reduced shrinkage
- Decreased breaking strength
- Improved adsorption
- Silky luster in appearance
Tenter
Jacquard varieties are all sizing to different degrees before calendering, so that the sizing can be attached to the surface of the fiber and prevent the cloth door pair from retracting. Sizing has a softening effect and promotes fiber-to-fiber friction.
Printing
There are currently two widely used printing methods, rotary screen and flat screen printing. Due to the small tension, it is not easy to deform, the color is bright, the color is full, and the screen printing defect is less, especially suitable for the production of multiple varieties. Rotary screen and flat screen printing, from the device point of view, all need screens, which originate from stencil printing, which is a printing method of carving hollow patterns out of paper plates, metal plates or chemicals.
Round screens are made of nickel round metal, while flat screens are screens stretched over a metal or wooden rectangular frame. Flat screen printing is divided into manual (table printing) and mechanical (flat screen printing). Due to different printing methods, the size is relatively within a certain allowable range, and the flat screen size is 305~1200mm. The circumference of the general rotary screen printing net is 640mm 820mm1018mm.
Steaming, soaping
Steaming: After textile printing, except for ice dyes and soluble vat dyes, general dyes must be steamed.
Purpose: To make printed textiles complete the moisture absorption and temperature rise of fibers and color paste film, accelerate the reduction of dyes and dissolve on fibers, make dyes diffuse into fibers and fix on fibers, and diffuse into fibers to produce color fixing.
Soaping: It is a very necessary and important process after steaming. During the soaping process, the soaping agent TS-618 has a physical and chemical interaction with the dye, and uses the dispersion, suspension, and complexation of the soaping agent to prevent it from sticking to the fabric, so as to improve the soaping fastness and anti-staining
Shrunk finishing
During the printing and dyeing process, the fabric is stretched by mechanical tension and there is internal stress. When the fabric is wet, the internal stress relaxes, which will form a shrinkage effect. Therefore, in actual production, the fabric must be mechanically pre-shrunk to reduce the cotton fabric. The shrinkage rate can stabilize the size of the finished product, keep the fabric width neat, and increase the added value of the product.
Calendering treatment
A process of fabric finishing. Using the physical plasticity of fibers under high pressure or high temperature conditions to flatten or roll out patterns on the surface of the fabric to increase the luster of the fabric. Similar to ironing, the method of flattening and ironing the surface can make the fabric have a special luster, increase the brightness of the fabric, and make the fabric have a good drape and smoothness.