Pack dyeing has low loss, high quality, fast delivery and good benefit. However, the polyester pack dyeing process is complicated, and there are many influencing factors that are difficult to control, and a little negligence may easily cause color blooms. Based on years of industry experience, Tiansheng Chemical discussed the uneven dyeing problem in polyester yarn dyeing.
Influencing factors of uneven dyeing and their control:
(1) Before the dyeing of the loose tube polyester cheese, the loose tube is firstly loosened, and the stainless steel spring tube is the first choice for the loose tube.
- Its advantage is that the effective penetrating area is particularly large, which is very beneficial to obtain level dyeing; it can be compressed freely, and has strong adaptability to orders of different batch numbers. The winding density of the bobbin is very important.
- Considering the head height of the dyeing mechanical pump, the winding density of the polyester bobbin yarn is preferably 0.33-0.39 g/cm3. If the winding is too tight, it is difficult for the dyeing solution to penetrate through the thick yarn layer, and the local color is lighter due to too little contact with the dye, resulting in uneven dyeing; if the winding is too loose, the bobbin is easy to deform and fall off, resulting in disordered yarn, making it difficult to machine .
(2) The purpose of the pre-treatment is to remove the oily agent stained on the yarn during the pre-spinning and cylinder dyeing process of the polyester yarn. Usually, the scouring agent TS-GLT is used, and soda ash is added, at 80 ° C. Conditions for 20 min. It must be noted that it must be cleaned after pre-treatment, otherwise it will easily cause uneven dyeing.
(3) In the selection of dyes, low-temperature dyes with small molecular weight and excellent dispersibility should be selected. Disperse red E-4B, yellow E-3RL, and blue E-4R are a group of low-temperature dyes that match well. most common chromatographic systems. Considering the prohibition on the use of dyes containing carcinogens, using Disperse Yellow SE-4RL instead of Disperse Yellow E-3RL can also achieve satisfactory dyeing results. For products with particularly high requirements for sublimation fastness, high-temperature disperse dyes are required. Red S-5BL, orange S-4RL, and blue S-3BG are often used. Most colors can be spelled out, and the cost is relatively low, but it needs to be added The amount of dispersant should be large, otherwise the dye will aggregate and cause staining, which is difficult to remove.
4) Selection of auxiliaries The selection of a leveling agent requires small foam, good dispersion at high temperature, and strong migration. TS-302 can prevent the color flower caused by the color difference between the inside and the outside of the package, and the usual dosage is 0.5-1 g/L. Cheese dyeing has extremely high requirements on water quality. The chelating dispersant TS-GSA has a strong chelating ability for Ca2+ and M92+ in water. The usual dosage is 0.5-1 g/L, which can not only reduce the hardness of water, but also It can increase the dispersing ability of dyes and prevent dyes from aggregating on yarns to form dye spots.
(5) It is best to control the pH value of the dyeing bath at 4.5-5.0.
(6)Control of the liquid flow The control of the direction of the liquid flow depends on the pressure of the pump. Generally, dyeing is carried out by clockwise circulation for 3 minutes and counterclockwise circulation for 4 minutes, and the color of the inside and outside of the bobbin is basically the same.
(7) Control of heating rate When the dyeing temperature is below 85°C, the dye is rarely dyed and the temperature can be raised directly. 85-110°C is the area where the dyeing speed increases the fastest, and it is necessary to strictly control the heating rate below 1.5°C/min; within the range of 115-130°C, it can be controlled at about 2°C/min. The heating curve of high temperature and high pressure cheese dyeing is as follows:
- 130°C for 40 minutes is for medium and dark colors, light colors can be appropriately shortened, and dark colors can be extended appropriately. The holding time should be appropriate, if it is too short, it will cause ring dyeing, and if it is too long, it will easily produce wool.
- Cool down quickly after dyeing, because condensation will be produced during the slow cooling process, and it is difficult to remove if it remains on the surface of the yarn.
(8) The soaping agent can wash off the disperse dyes adsorbed on the surface of the yarn, so that the color fastness can be guaranteed, and it can also remove other substances adsorbed on the surface of the yarn during the dyeing process.
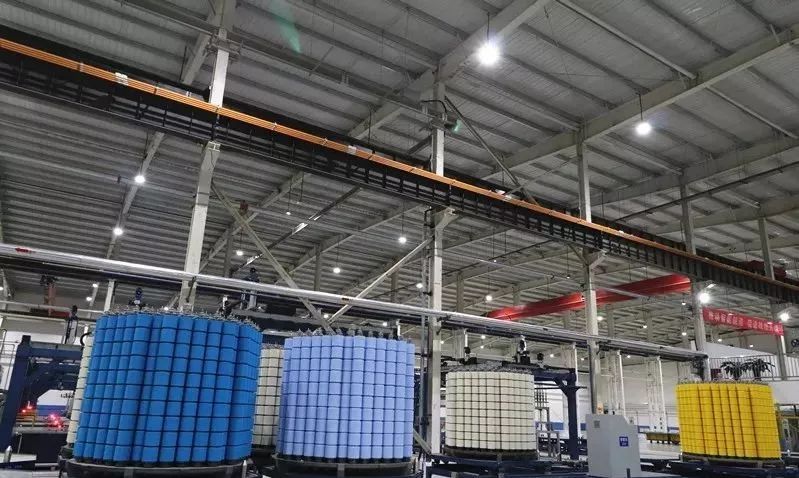